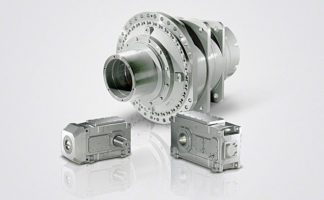
13/18
Siemens D 21.4 · 2017
Tools and configuration
Configuration notes
SINAMICS S120 Control Units
13
■
Configuration
(continued)
SINAMICS S performance characteristics
1)
The high output frequency option is required to enable output frequencies
above 550 Hz.
For additional information see section Control Units, and on the Internet at
Characteristics
Servo Control
Vector Control
V/f control
Notes
Typical application
• Drives with high dynamic
motion control
• Angular-locked synchronism
with isochronous PROFIBUS/
PROFINET in conjunction
with SIMOTION
• For use in machine tools
and clocked production
machines
• Variable-speed drives with
high speed and torque
stability in general machinery
construction
• Especially suitable for
induction motors and
reluctance motors (1FP1)
• Drives with low requirements
on dynamic response and
精度
• Group drives running with a
high degree of precision, e.g.
on textile machines with
SIEMOSYN motors
Mixed operation of Servo
Control and Vector Control is
not possible on CU320-2.
Mixed operation is possible for
V/f control modes.
Dynamic response
Very high
High
Low
Highest dynamic response
with 1FK7 High Dynamic
synchronous motors and
Servo Control.
Control modes with encoder
Position control/
Speed control/
Torque control
Position control/
Speed control/
Torque control
None
SIMOTION D with Servo
Control is standard for motion
control.
Control modes without
encoder
Speed control
Speed control/torque control
All V/f control modes
With Servo for induction
motors only.
With V/f control, the speed can
be kept constant by means of
selectable slip compensation.
Asynchronous motor
(在duction motor)
Synchronous motor
Reluctance motor (1FP1)
Torque motor
Linear motor
Yes
Yes
No
Yes
Yes
Yes
Yes
Yes
Yes
No
Yes
No
No
No
No
V/f control (textiles) is
recommended for
SIEMOSYN motors.
Permissible ratio of motor
rated current to rated current
of Motor Module
1:1 to 1:4
1.3:1 to 1:4
1:1 to 1:12
For Servo Control and Vector
Control, maximum control
quality up to 1:4. Between 1:4
and 1:8, increasing restric-
tions regarding torque and
rotational accuracy. V/f con-
trol is recommended for < 1:8.
Maximum number of
parallel-connected motors
per Motor Module
4
8
Unlimited in theory
Motors with identical power
ratings can only be connected
in parallel if they are induction
motors.
With V/f Control, the motors
可以有不同t power
ratings.
Setpoint resolution position
controller
31 bit + sign
31 bit + sign
- - - - - -
Setpoint resolution speed/
frequency
31 bit + sign
31 bit + sign
0.001 Hz
Setpoint resolution torque
31 bit + sign
31 bit + sign
- - - - - -
Maximum output frequency
Values valid for the factory set-
ting High output frequencies
can only be achieved when
using suitable motors and the
appropriate parameterization.
For synchronous motors,
observe the voltage limit
(2 kV) and use a VPM module.
Only for induction motors:
When using edge modulation,
600 Hz is possible at 4 kHz, or
300 Hz at 2 kHz and
200 Hz at 1.25 kHz.
• For current controller clock
cycle/pulse frequency
660 Hz
1)
与125年
μ
s/4 kHz
330 Hz
with 250
μ
s/4 kHz
400 Hz
with 250
μ
s/4 kHz
• For current controller clock
cycle/pulse frequency
(chassis frame sizes FX
and GX)
330 Hz
with 250
μ
s/2 kHz
160 Hz
with 250
μ
s/2 kHz
200 Hz
with 250
μ
s/2 kHz
• For current controller clock
cycle/pulse frequency
(chassis frame sizes HX
and JX)
Not permitted
100 Hz
with 400
μ
s/1.25 kHz
100 Hz
with 400
μ
s/1.25 kHz
Maximum field weakening
With Servo Control combined
with encoder and appropriate
special motors, field weaken-
ing up to 16 times the field-
weakening threshold speed is
possible.
These values refer to
1FT7/1FK7 synchronous
motors.
Note voltage limit (
k
E
factor)
for third-party motors.
• For asynchronous
(在duction) motors
5 times
5 times
4 times
• For synchronous motors
2 times
2 times
- - - - - -
• For reluctance motors
(1FP1)
- - - - - -
2 times
- - - - - -
© Siemens AG 2017