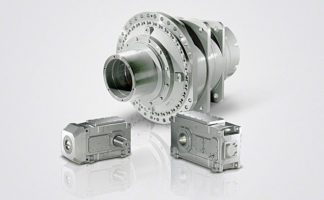
7/9
Siemens D 21.4 · 2017
SINAMICS S120 drive system
Control Units
7
■
Overview
(continued)
Extended technology with SIMOTION
SIMOTION D Control Units support the coordinated motion
control of multiple drives. Technology objects are implemented
in addition to drive objects on these Control Units. These are
grouped to form technology packages and make available
extended motion control functions (e.g. synchronous operation,
cam disk, path interpolation and others) or technological func-
tions (e.g. a cam controller, a temperature or pressure control).
The IEC 61131-3-compliant PLC integrated in SIMOTION D
Control Units means that they are not just capable of controlling
sequences of motions, but the entire machine including HMI and
I/Os.
You can obtain further information about SIMOTION in the
Industry Mall and Catalog PM 21.
Comprehensive package of open-loop and closed-loop control functions
A wide variety of standard functions such as setpoint input, data
set changeover, controller optimization and kinetic buffering en-
sure a high degree of functional reliability and excellent flexibility
of application.
Overview of key open-loop and closed-loop control functions
SINAMICS S120
closed-loop control modes
SINAMICS S120
open-loop control modes
Main functions
SINAMICS S120
for booksize/chassis
Comment,
note
Infeed Control
• Booksize
-
Current control
with/without mains sensor
-
V
DC
control
without/with mains sensor
• Chassis
-
Current control
with mains sensor
-
V
DC
control
with mains sensor
• Booksize/chassis
-
Basic Mode
Rectification only
-
Smart Mode
Rectification and
regenerative feedback
• Mains identification
• Controller optimization
• Harmonics filter
• Automatic restart
The mains sensor is the
VSM 10 Voltage Sensing
模块;“当前”是line
current; 3-phase with line
frequency
Vector Control
• Asynchronous (induction)
motor
-
Torque control
with/without encoder
-
Speed control
with/without encoder
• Torque motor
-
Torque control
with encoder
-
Speed control
with/without encoder
• Asynchronous (induction)
motor,
torque motor
-
Position control
with encoder
• Reluctance motor
-
Torque control
with/without encoder
-
Speed control
with/without encoder
• Linear/parabolic
characteristic
• Fixed-frequency
characteristic (textile)
• Independent voltage
setpoint input
• Data set changeover
• Extended setpoint input
• Motor identification
• Current/speed controller
optimization
• Technology controller
• Basic positioner
• Automatic restart
• Flying restart with/without
encoder
• Kinetic buffering
• Synchronization
• Droop
• Brake control
Mixed operation with V/f con-
trol modes is possible; it is for
this reason that the V/f control
modes are stored only once in
the "Vector control" drive
object.
V/f is not possible for reluc-
tance motors.
Catalog D 81.1 provides
additional information about
reluctance motors
.
Position control can be
selected as a function module
from both the servo and vector
modes.
Synchronous motors (1FK and
1FT) and linear motors can be
operated only in Servo mode.
Servo Control
• Asynchronous induction
motor
-
Torque control
with encoder
-
Speed control
with/without encoder
• Synchronous motor,
linear motor and
torque motor
-
Torque control
with encoder
-
Speed control
with encoder
• All motor types
-
Position control
with encoder
• Linear/parabolic
characteristic
• Fixed-frequency
characteristic (textile)
• Independent voltage
setpoint input
• Data set changeover
• Setpoint input
• Motor identification
• Damping application
• Technology controller
• Basic positioner
• Brake control
Mixed operation with V/f con-
trol modes is possible; it is for
this reason that the V/f control
modes are only saved once in
the "Vector control" drive
object.
Position control can be
selected as a function module
from both the servo and vector
modes.
© Siemens AG 2017