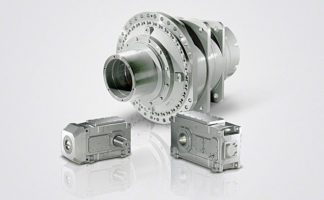
3./5
Siemens D 21.4 · 2017
Safety Integrated
Safety Integrated
3.
■
Function
Safe Stop 2 (SS2)
The SS2 function brings the motor to a standstill quickly and
safely and then activates the SOS function once the motor has
stopped.
Effect
The Safe Stop 2 function can safely stop the drive in accordance
with EN 60204-1, Stop Category 2. When the SS2 function is
selected, the drive brakes autonomously along a quick stop
ramp. In contrast to SS1, the drive control remains operational
afterwards, i.e. the motor can supply the full torque required to
maintain zero speed. Standstill is safely monitored (Safe
Operating Stop function).
Application
As with SS1, the SS2 function ensures the quickest possible
deceleration of the motor. However, the motor power is not
switched off. Instead, a control system prevents it from leaving
the standstill position – even if it is affected by external forces.
Typical applications for SS2 include machine tools, for example.
Customer benefits
The SS2 function ensures a rapid axis stop. Because the control
remains active, after the safety function is deselected, productive
operation can continue without referencing. This ensures short
设置和standstill times and high productivity.
Safe Operating Stop (SOS)
With the SOS function, the stopped motor is held in position by
the drive control system and its position monitored.
Effect
The SOS function constitutes safe standstill monitoring. The
drive control remains in operation. The motor can therefore
deliver the full torque to hold the current position. The actual
position is reliably monitored. In contrast to safety functions SS1
and SS2, the speed setpoint is not influenced autonomously.
After SOS has been activated, the higher-level control must
bring the drive to a standstill within a parameterized time and
then hold the position setpoint.
Application
SOS is an ideal solution for all those applications for which the
machine or parts of the machine must be at a safe standstill for
certain steps, but the drive must also supply a holding torque.
It is ensured that despite counter torque the drive remains in its
current position. In contrast to SS1 and SS2, the drive does not
brake autonomously in this case. It expects the higher-level con-
troller to ramp down the relevant axes as a coordinated group
within an adjustable delay time. This can be used to prevent any
damage to the machine or product. Typical applications for SOS
include winders, converting and packaging machines and
machine tools.
Customer benefits
No mechanical components are necessary to keep the axis in
position despite any counterforce that may occur. Due to the short
switching times and the fact that the drive control always remains
active, setup and downtimes are reduced. Recalibration of the
axis after exiting the SOS function is not necessary. The axis can
immediately be moved again after deactivation of the SOS
function.
v
t
G_D211_XX_00306
SOS
G_D211_XX_00207
s
t
SOS
∆t
© Siemens AG 2017