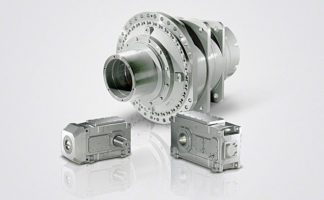
2/10
Siemens D 11 · 2015
■
Function
(continued)
2
Highlights
Safety Integrated
安全集成功能手册包含添加itional information about the encoderless safety functions.
The safety functions are listed below with criteria for actual value
sensing
Safe speed/position sensing with encoder
Incremental encoders or absolute encoders with photoelectric
sampling are permitted for safe sensing of the position values on
a drive. HTL/TTL incremental encoders may also be used.
Safe actual value sensing relies on redundant evaluation of the
incremental tracks A/B that supply sin/cos signals of 1 V
pp
. Only
encoders of the type whose A/B track signals are created and
processed using purely analog techniques can be used. The en-
coder signals are input via the SMC20 Sensor Module Cabinet-
Mounted.
For HTL/TTL incremental encoders, safe actual value sensing is
achieved by using two independent encoders. The minimum
possible speed resolution must also be taken into account. The
encoder signals are input via the SMC30 Sensor Module Cabi-
net-Mounted.
When motors with a DRIVECLiQ interface are used, the speed/
position actual values are generated directly in the motor as safe
values and transferred to the Control Unit over a safe DRIVECLiQ
communication link.
The following can be used for safe speed/position sensing:
•
Single-encoder systems or
•
2-encoder systems
Example: Single-encoder system
In a single-encoder system, the motor encoder is used exclu-
sively for safe actual value sensing. An incremental encoder or
absolute encoder with photoelectric sampling must be used in
this case.
Example: Dual-encoder system
In the case of the 2-encoder system, the safe actual values for a
drive are provided by two separate encoders. The actual values
are transferred to the Control Unit over DRIVE-CLiQ. When
motors without a DRIVE-CLiQ connection are used, a Sensor
Module (SMC20/30, SME20/25/120/125) must be provided.
Each measuring system requires a separate DRIVE-CLiQ con-
nection.
For this configuration, either two HTL/TTL encoders, one dual-
HTL / TTL encoder or one HTL/TTL encoder and one sin/cos en-
coder can be used.
1)
The use of this safety function without encoder is permitted only on request
and only for induction motors or synchronous motors of the SIEMOSYN
series.
Functions
Abbreviation
With encoder
Without encoder
Description
Basic Functions
Safe Torque Off
STO
Yes
Yes
Safe Torque Off
Safe Stop 1
SS1
Yes
Yes
Safe Stop according to stop category 1
Safe Brake Control
SBC
Yes
Yes
Safe Brake Control
Extended Functions
Safe Torque Off
STO
Yes
Yes
1)
Safe Torque Off
Safe Stop 1
SS1
Yes
Yes
1)
Safe Stop according to stop category 1
Safe Brake Control
SBC
Yes
Yes
1)
Safe Brake Control
Safe Operating Stop
SOS
Yes
No
Safe monitoring of the standstill position
Safe Stop 2
SS2
Yes
No
Safe Stop according to stop category 2
Safely-Limited Speed
SLS
Yes
Yes
1)
Safe monitoring of the maximum speed
Safe Speed Monitor
SSM
Yes
Yes
1)
Safe monitoring of the minimum speed
Safe Direction
SDI
Yes
Yes
1)
Safe monitoring of the direction of
motion
Safely-Limited Position
SLP
Yes
No
Safely-limited position
Safe Position
SP
Yes
Yes
Safe transfer of position values
Safe Brake Test
SBT
Yes
No
Safe test of the required holding torque
of a brake
DRIVE-CLiQ
E
M
G_D011_EN_00442
Machine table
Backlash
Sensor Module
(not applicable for motor
with DRIVE-CLiQ interface)
E = encoder
M = motor
E
M
E
DRIVE-CLiQ
G_D011_EN_00443
Sensor Module
(not applicable for motor
with DRIVE-CLiQ interface)
E = encoder
M = motor
© Siemens AG 2015