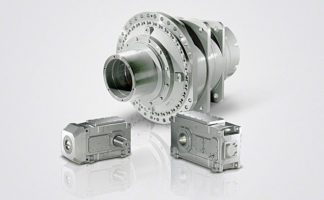
2/9
Siemens D 35 · 2017
2
Communication
EtherNet/IP
■
Overview
Ethernet Industrial Protocol (EtherNet/IP) is an open standard for
industrial networks. EtherNet/IP is used to transmit cyclic I/O
data and acyclic parameter data. EtherNet/IP was developed by
罗克韦尔自动化和ODVA(打开设备网Vendor
Association), and belongs to the international standard series
IEC 61158. EtherNet/IP is a popular communication standard,
particularly in the American market and in the Rockwell control-
lers environment.
■
Overview
BACnet MS/TP (
B
uilding
A
utomation and
C
ontrol
Net
works
M
aster-
S
lave/
T
oken
P
assing) is another fieldbus system based
on the physical characteristics of RS485, which is mainly used in
the field of building automation. BACnet MS/TP defines a variety
of services including data utilization, alarm processing, event
handling, processing of value changes, device and network
management, as well as various types of objects. Interopera-
bility is ensured by means of a uniform approach to services and
procedures, which is laid down in "application profiles". These
profiles are available for a wide range of applications. The
SINAMICS G120P converters, especially developed for fluid
flow machines (such as pumps, fans and compressor drives),
use the application profile "BACnet application-specific
controller" in building automation.
■
Overview
As a simple fieldbus protocol, Modbus RTU can be used both
cyclically and acyclically. Based on RS485 physical bus charac-
teristics, up to 32 nodes can be networked to one bus segment
and connected to a higher-level controller. This protocol is gen-
erally used when there are limited demands on data throughput.
■
Overview
As a simple fieldbus protocol, USS (
U
niversal
S
erial
I
nterface
protocol of Siemens AG, 1992) can be used both cyclically and
acyclically. Based on RS485 physical bus characteristics,
up to 32 nodes can be networked to one bus segment and
connected to a higher-level controller. This protocol is generally
used when there are limited demands on data throughput.
■
Overview
P1 is an asynchronous master-slave communication between
what is known as a Field Cabinet (master) and the FLN devices
(slaves). FLN stands for
F
loor
L
evel
N
etwork. The master individ-
ually addresses the various slaves. A slave responds only if the
master addresses it. Communication between the slaves is not
possible.
A Field Cabinet can have several FLN ports. Up to 32 FLN
devices (slaves) can be connected to each FLN port.
BACnet MS/TP
Modbus RTU
USS
FLN P1
© Siemens AG 2017