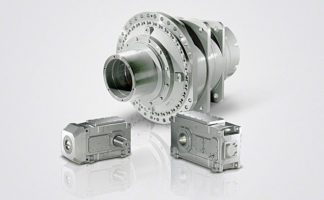
5/6
Siemens D 35 · 2017
■
Function
(continued)
5
SINAMICS G120P Cabinet, converter cabinet units
SINAMICS G120P Cabinet, 75 kW to 630 kW
SINAMICS G120P Cabinet
Software and protective functions
The software functions available as standard are described
below:
Software and protective functions
Description
Setpoint input
The setpoint can be input both internally and externally. It is applied internally as a fixed setpoint, motorized
potentiometer setpoint or jog setpoint and externally via the communications interface or an analog input on the
customer terminal block. The internal fixed setpoint and the motorized potentiometer setpoint can be switched
over or adjusted using control commands from any interface.
Motor identification
The automatic motor identification function makes commissioning faster and easier and optimizes closed-loop
control of the drive.
Ramp-function generator
An advanced ramp-function generator with separately adjustable ramping times, together with adjustable
rounding times in the lower and upper speed ranges, allows the drive to be smoothly accelerated and braked.
As a consequence, this avoids the drive train from being overloaded and reduces the stress on mechanical
components. The down ramps can be parameterized separately for quick stop.
V
dc max
controller
The V
dc max
controller automatically prevents overvoltages in the DC link if the set down ramp is too short, for
example. This may also extend the set ramp-down time.
Kinetic buffering (KIP)
In the event of supply voltage dips, the kinetic energy of the rotating drive is used to buffer the DC link so as to
防止错旅行。转换器仍然工作onal as long as the drive can provide regenerative energy as a
result of its motion and the DC link voltage does not drop below the trip threshold. When the line supply recovers
within this time, the drive is again accelerated up to its setpoint speed.
Automatic restart
1)
The automatic restart switches the drive on again when the power is restored after a power failure, and ramps up
to the current speed setpoint.
Flying restart
1)
The "Flying restart" function allows the converter to be switched to a motor that is still turning.
Technology controller
The technology controllers (in the form of PID controllers) can be used to implement simple closed-loop control
functions.
A PID controller controls the motor speed as a process controller for temperature, pressure, air quality or fill
levels. Three further PID controllers are freely programmable. The P, I, and D component can be disabled.
Free function blocks
Using the freely programmable function blocks, it is easy to implement logic and arithmetic functions for con-
trolling the SINAMICS G120P Cabinet unit. The blocks can be programmed by means of an operator panel or the
STARTER commissioning tool.
I
²
t
detection for motor protection
A motor model stored in the converter software calculates the motor temperature based on the current speed and
load. More exact sensing of the temperature, which also takes into account the influence of the ambient tempera-
ture, is possible by means of direct temperature sensing using KTY sensors in the motor winding.
Motor temperature evaluation
Motor protection by evaluating a temperature sensor of type KTY, PTC, Pt1000 or bimetal NC contact. When a
KTY sensor is connected, the limit values can be set for warning or shutdown. When a PTC thermistor is con-
nected, the system reaction to triggering of the thermistor (alarm or shutdown) can be defined.
Motor blocking protection
A blocked motor is detected and protected against thermal overloading by a fault trip.
Multi-zone control
Closed-loop control of a zone with up to 3 sensors for pressure or temperature, or closed-loop control of two
independent zones each with one sensor.
Essential service mode
Special converter operating mode that enhances the availability of the drive system in the event of a fire.
Bypass
2)
When the setpoint is reached or a fault occurs, there is a changeover to mains operation.
Cascade connection
2)
Load-dependent connection and disconnection of a maximum of three additional motors by the converter in
order to provide a largely constant output power.
Hibernation mode
Startup or shutdown of the drive when the relevant value drops below an external setpoint or the internal
PID控制器roller setpoint
Power unit protection
Description
Ground fault monitoring at output end
A ground fault at the output end is detected by a summation current monitor and results in shutdown in grounded
systems.
Electronic short-circuit protection at the
output end
A short-circuit at the output end (e.g. at the converter output terminals, in the motor cable or in the motor terminal
box) is detected and the converter shuts down with "fault".
Thermal overload protection
An alarm is issued first when the overtemperature threshold responds. If the temperature rises further, the unit
independently adjusts the pulse frequency or output current so that a reduction in the thermal load is achieved.
Once the cause of the fault has been eliminated (e.g. cooling has been improved), the original operating values
are automatically resumed.
1)
工厂setting: not activated (can be parameterized).
2)
This function requires an additional external circuit.
© Siemens AG 2017