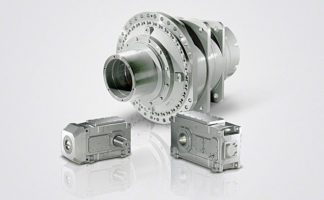
SINAMICS DCM
DC Converter and Control Module
General information
3/5
西门子D 23.1 · 2014
3
■
Function
(continued)
Function
Description
Functions of the closed-loop control in the armature circuit
(continued)
Speed controller
The speed controller compares the setpoint and actual value of the speed and if there is a deviation, enters an appropri-
ate current setpoint into the current controller (principle: Speed control with lower-level current controller). The speed
controller is implemented as PI controller with additional D component that can be selected. Further, a switchable droop
function can be parameterized. All of the controller parameters can be adjusted independently of one another. The value
for
K
p
(gain) can be adapted depending on a connector signal (external or internal).
In this case, the P gain of the speed controller can be adapted depending on the speed actual value, current actual
value, setpoint-actual value distance or the wound roll diameter. This can be pre-controlled in order to achieve a high
dynamic performance in the speed control loop. For this purpose, e.g. depending on the friction and the moment of
inertia of the drive, a torque setpoint signal can be added after the speed controller. The friction and moment of inertia
compensation are determined using an automatic optimization run.
The output quantity of the speed controller can be directly adjusted via parameter after the controller has been enabled.
Depending on the parameterization, the speed controller can be bypassed and the converter controlled either with
closed-loop torque or current control. In addition, it is also possible to switch between speed control/torque control in
operation using the "leading/following switchover" selection function. The function can be selected as binector using a
binary user-assignable terminal or a serial interface. The torque setpoint is input via a selectable connector and can
therefore come from an analog user-assignable terminal or via a serial interface.
A limiting controller is active when in the following drive state (torque or current controlled operation). In this case,
depending on a speed limit that can be selected using parameters, the limiting controller can intervene in order to
prevent the drive accelerating in an uncontrolled fashion. In this case, the drive is limited to an adjustable speed
deviation.
Torque limiting
The speed controller output represents the torque setpoint or current setpoint depending on what has been parameter-
ized. In torque-controlled operation, the speed controller output is weighted with the machine flux
Φ
and transferred to a
current limiting stage as a current setpoint. Torque control is applied primarily in field weakening operation in order to
limit the maximum motor torque independent of the speed.
The following functions are available:
• Independent setting of positive and negative torque limits using parameters.
• Switchover of the torque limit using a binector as a function of a parameterizable switchover speed.
• Free input of a torque limit by means of a connector signal, e.g. via an analog input or via serial interface.
The lowest specified quantity should always be effective as the actual torque limit. Additional torque setpoints can be
added after the torque limit.
Current limiting
The current limit that can be adjusted after the torque limit is used to protect the converter and the motor. The lowest
specified quantity is always effective as the actual current limit.
The following current limit values can be set:
• Independent setting of positive and negative current limits using parameters (maximum motor current setting).
• Free input of a current limit using a connector, e.g. from an analog input or via a serial interface.
• Separate setting of current limit using parameters for stopping and quick stop.
• Speed-dependent current limiting: An automatically initiated, speed-dependent reduction of the current limit at high
speeds can be parameterized (commutation limit curve of the motor).
I
2
t
monitoring of the power section: The thermal state of the thyristors is calculated for all current values. When the
thyristor limit temperature is reached, the unit responds as a function of parameter settings, i.e. the converter current is
reduced to the rated DC current or the unit is shut down with a fault message. This function is used to protect the
thyristors.
Current controller
The current controller is implemented as PI controller with P gain and integral time that can be set independently from
one another. The P and I components can also be deactivated (pure P controller or pure I controller). The current actual
value is sensed using a current transformer on the three-phase side and is fed to the current controller via a load resistor
and rectification after analog-digital conversion. The resolution is 10 bits for the converter rated current. The current limit
output is used as current setpoint.
The current controller output transfers the firing angle to the gating unit – the pre-control function is effective in parallel.
Pre-control
The pre-control in the current control loop improves the dynamic performance of the closed-loop control. This allows rise
times of between 6 and 9 ms in the current control loop. The pre-control is effective dependent on the current setpoint
and EMF of the motor and ensures – for intermittent and continuous current or when the torque direction is reversed –
that the required firing angle is quickly transferred as setpoint to the gating unit.
Auto-reversing module
In conjunction with the current control loop, the auto-reversing module (only for units with four-quadrant drives) ensures
逻辑sequence of all of the operations and processes required to change the torque direction. The torque direction
can also be disabled when required via parameter.
Gating unit
The gating unit generates the firing pulses for the power section thyristors in synchronism with the line supply voltage.
The synchronization is independent of the speed and the electronics supply and is sensed at the power section. The
timing of the firing pulses is defined by the output values of the current controller and the pre-control. The firing angle
limit can be set using parameters.
在一个频率范围45 to 65 Hz, the gating unit automatically adapts itself to the actual line frequency.
© Siemens AG 2014