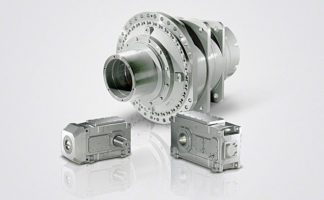
SINAMICS DCM
DC Converter and Control Module
General information
3/4
Siemens D 23.1 · 2014
3
■
Function
Function
Description
Functions of the closed-loop control in the armature circuit
Speed setpoint
The source of the speed setpoint and additional setpoints can be freely selected by making the appropriate parameter
settings:
• Entered using analog values 0 to
±
10 V, 0 to
±
20 mA, 4 to 20 mA
• Entered via the PROFIBUS fieldbus interface, Ethernet interface for PROFINET (optional)
• Using the integrated motorized potentiometer
• Using binectors with the functions: Fixed setpoint, jogging, crawl
• Entered via serial interfaces of the SINAMICS DC MASTER
• Entered via supplementary modules
实现扩展,这样100%定位点(formed from the main setpoint and supplementary setpoints) corresponds
to the maximum motor speed.
The setpoint can be limited to a minimum and maximum value via a parameter or connector. Further, additional points
are provided in the firmware e.g. in order to be able to enter supplementary setpoints before or after the ramp-function
发电机. The "setpoint enable function" can be selected using a binector. After a parameterizable filter function (PT1
element), the summed setpoint is transferred to the setpoint input of the speed controller. In this case, the ramp-function
发电机is also active.
Actual speed
One of four sources can be selected as signal for the speed actual value.
•
Analog tachometer
The voltage of the tachogenerator at maximum speed can be between 8 and 270 V. Adaptation to the voltage is realized
using parameters.
•
Pulse encoder
The pulse encoder type, the number of pulses per revolution and the maximum speed are set using parameters.
Encoder signals (symmetrical: with additional, inverted track, unsymmetrical: referred to ground) up to a maximum
differential voltage of 27 V can be processed by the evaluation electronics.
The rated voltage range (5 or 15 V) for the encoder is selected via parameters. The power supply for the pulse encoder
can be taken from the DC Converter for a rated voltage of 15 V.
5 V encoders require an external power supply. The pulse encoder is evaluated across the three tracks:
Track 1, track 2 and zero mark. However, pulse encoders without zero mark can also be used. A position actual
value can be sensed using the zero mark. The maximum frequency of the encoder pulses can be 300 kHz. It is
recommended that pulse encoders with at least 1024 pulses per revolution are used (due to the smooth running
operation at low speeds).
•
Operation without tachometer with EMF control
A speed actual value encoder is not required for closed-loop EMF control. In this case, the output voltage of the device
is measured in the DC converter. The measured armature voltage is compensated by the internal voltage drop across
the motor (IR compensation). The level of compensation is automatically determined during the current controller
optimization run. The accuracy of this control method, which is defined by the temperature-dependent change in the
motor armature circuit resistance, is approximately 5 %. We recommend that the current controller optimization run is
repeated when the motor is in the warm operating condition to achieve a higher degree of precision. The closed-loop
EMF control can be used if the requirements on the precision are not so high, if it is not possible to mount an encoder
and the motor is operated in the armature voltage control range.
Notice: In this mode, EMF-dependent field weakening is not possible.
•
Freely selectable speed actual value signal
For this mode, any connector number can be selected as speed actual value signal.
This setting is especially selected if the speed actual value sensing is implemented on a supplementary technology
module.
Before the speed actual value is transferred to the speed controller, it can be smoothed using a parameterizable
smoothing element (PT1 element) and two adjustable bandstop filters. Bandstop filters are used primarily for the
过滤的目的esonant frequencies caused by mechanical resonance. The resonant frequency and the filter
quality factor can be set.
Ramp-function
发电机
When there is a step change in the setpoint applied at its input, the ramp-function generator converts the setpoint into a
signal with a steady rate of rise. Ramp-up time and ramp-down time can be selected independently of one another. In
addition, the ramp-function generator has initial and final rounding-off (jerk limiting) that are effective at the beginning
and end of the ramp-up time.
All of the times for the ramp-function generator can be set independently of one another.
Three parameter sets are available for the ramp-function generator times; these can be selected via binary select inputs
or a serial interface (via binectors). The ramp-up function generator parameters can be switched over in operation.
In addition, a multiplication factor can be applied to the value of parameter set 1 via a connector (to change the ramp-
function generator data via a connector). When entering ramp-function generator times with the value zero, the speed
setpoint is directly input into the speed controller.
© Siemens AG 2014