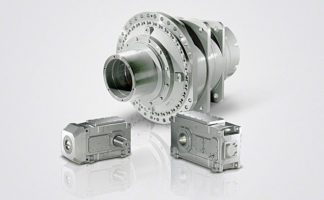
FLENDER Standard Couplings
Torsionally Rigid All-Steel Couplings — ARPEX ARS-6 Series
Further hubs and flanges
Clamping hub
6/24
Siemens MD 10.1 · 2015
6
■
Selection and ordering data
Standard clamping hub types 124 and 125 can be combined
with any spacer. It should be noted that the clamping hub can
be used only as an "N hub" (hub core outside). Clamping hub as
"B hub" (hub core in spacer tube) on request. Transmissible
torque and maximum bore diameter are smaller on a B hub vari-
ant than stated below.
Function
ARPEX clamping hubs transmit torque with the aid of a flexible
press fit. By pulling the clamping ring on by means of the tight-
ening screws the necessary surface pressure is applied in the
"shaft/hub" contact area. After the tightening operation the
clamping ring lies up against the clamping hub. The gap dimen-
sion between the clamping hub and the clamping ring is then
zero. This has the effect that even with repeated fitting and dis-
mounting the balancing condition is maintained (no wobble ef-
fect). Clamping hubs can be clamped as often as required. It
必须保证锥表面adequa吗tely lubri-
cated.
Transmissible torque
The clamping connections are designed to enable the specified
maximum torques to be transmitted. These maximum torques
may not be exceeded. The mathematical coefficient of friction
between the shaft and the clamping hub is
μ
= 0.16.
Fitting clearance and surface roughness
The transmissible torques take into account the maximum fitting
clearance and maximum surface roughness. For other shaft tol-
erances reduced torques or other bore tolerances must be used.
The surface roughness of the shaft should be
≤
R
a
= 1.6
μ
m.
The shaft tolerance must be specified in the order.
To specify, "-Z" must be added to the article number and the
order code "Y26" with plain text specification of the shaft
tolerance for D1 must be added as well. The fit pairing G6/h6
should be used wherever possible.
Type 125
Type 124
G_MD10_EN_00152
ØND1
ØD1
NL
L2
ØDA
ØDA
NL
A
L2
ØND1
ØD1
Size
Clamping
hub
Dimensions in mm
Mass moment
of inertia
Article No.
Weight
Order codes for bore
diameters and toler-
ances
are specified in
catalog section 3
DA
Type
D1
D1
ND1
NL
L2
A
J
m
mm
min.
max.
kgm
2
kg
78-6
124
15
25
48
35
19
6
0.0002
2LC0470-0LM90-0AA0
0.5
125
2LC0470-0LN90-0AA0
105-6
124
25
45
74
40
22
8
0.0012
2LC0470-1LM90-0AA0
1.0
125
2LC0470-1LN90-0AA0
125-6
124
30
50
86
45
28
8
0.0026
2LC0470-2LM90-0AA0
1.6
125
2LC0470-2LN90-0AA0
140-6
124
30
60
103
50
33
9
0.0051
2LC0470-3LM90-0AA0
2.4
125
2LC0470-3LN90-0AA0
165-6
124
38
70
118
55
33
9
0.0096
2LC0470-4LM90-0AA0
3.4
125
2LC0470-4LN90-0AA0
175-6
124
42
75
122
65
43
10
0.0141
2LC0470-5LM90-0AA0
4.3
125
2LC0470-5LN90-0AA0
195-6
124
48
75
135
70
44
9
0.0231
2 lc0470-6lm90-0aa0
6.2
125
2LC0470-6LN90-0AA0
210-6
124
55
85
141
75
49
9
0.0309
2LC0470-7LM90-0AA0
7.2
125
2LC0470-7LN90-0AA0
240-6
124
65
95
164
90
59
10
0.0648
2LC0470-8LM90-0AA0
11.4
125
2LC0470-8LN90-0AA0
© Siemens AG 2015