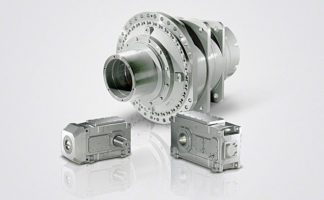
FLENDER Standard Couplings
Technical Information
2/6
Siemens MD 10.1 · 2015
2
Standards
Machines
Couplings
Balancing
Shaft-hub connections
Formula symbols
Key to the formula symbols
2006/42/EC
EC Machinery Directive
94/9/EC
ATEX Directive – Manufacturer – and ATEX Guideline to
Directive 94/9/EC
2014/34/EU
ATEX Directive – Manufacturer
1999/92/EC
ATEX Directive – Operator – and ATEX Guideline to
Directive 1999/92/EC
DIN EN 13463
Non-electrical设备用于潜在的交货plo-
sive atmospheres
DIN EN 1127
Explosive atmospheres, explosion prevention and pro-
tection
DIN EN 50347
General-purpose three-phase induction motors having
standard dimensions and outputs
DIN 740
Flexible shaft couplings Part 1 and Part 2
VDI Guideline 2240
Shaft couplings - Systematic subdivision according to
their properties VDI Technical Group Engineering
Design 1971
API 610
Centrifugal Pumps for Petroleum, Chemical and Gas
Industry Services
API 670
Machinery Protection System
API 671
Special Purpose Couplings for Petroleum, Chemical
and Gas Industry Services
ISO 10441
Petroleum, petrochemical and natural gas industries –
Flexible couplings for mechanical power transmission-
special-purpose applications
DIN ISO 1940
Requirements for the balancing quality of rigid rotors
DIN ISO 21940-32
Mechanical vibrations; standard governing
the type of parallel key during balancing of shafts and
composite parts
DIN 6885
Driver connections without taper action – parallel keys –
keyways
SAE J620d
Flywheels for industrial engines ...
DIN 6288
Internal-combustion piston engines
Connection dimensions and requirements for flywheels
and flexible coupling
ASME B17.1
Keys and keyseats
DIN EN 50347
General-purpose three-phase induction motors with
standard dimensions and output data
BS 46-1:1958
Keys and keyways and taper pins Specification
Name
Symbol
Unit
Explanation
Torsional stiffness,
dynamic
C
Tdyn
Nm/rad
For calculating torsional vibration
Excitation fre-
quency
f
err
Hz
Excitation frequency of motor or
driven machine
Moment of inertia
J
kgm
2
Moment of inertia of coupling sides 1
and 2
Axial misalignment
Δ
K
a
mm
Axial misalignment of the coupling
halves
Radial misalign-
ment
Δ
K
r
mm
Radial misalignment of the coupling
halves
Angular misalign-
ment
Δ
K
w
°
Angular misalignment of the coupling
halves
Service factor
FB
Factor expressing the real coupling
load as a ratio of the nominal cou-
pling load
Frequency factor
FF
Factor expressing the frequency
dependence of the fatigue torque
load
Temperature factor
FT
Factor taking into account the reduc-
tion in strength of flexible rubber
materials at a higher temperature
Weight
m
kg
Weight of the coupling
Rated speed
n
N
rpm
Coupling speed
Maximum coupling
speed
n
Kmax
rpm
Maximum permissible coupling
speed
Rated power
P
N
kW
Rated output on the coupling, usually
the output of the driven machine
Rated torque
T
N
Nm
Rated torque as nominal load on the
coupling
Fatigue torque
T
W
Nm
Amplitude of the dynamic coupling
load
Maximum torque
T
max
Nm
More frequently occurring maximum
load, e.g. during starting
Overload torque
T
OL
Nm
Very infrequently occurring maximum
load, e.g. during short circuit or
blocking conditions
Rated coupling
torque
T
KN
Nm
Torque which can be transmitted as
static torque by the coupling over the
period of use.
Maximum coupling
torque
T
Kmax
Nm
转矩可以频繁
transmitted (up to 25 times an hour)
as maximum torque by the coupling.
Coupling overload
torque
T
KOL
Nm
Torque which can very infrequently
be transmitted as maximum torque
by the coupling.
Fatigue coupling
torque
T
KW
Nm
Torque amplitude which can be
transmitted by the coupling as
dynamic torque at a frequency of
10 Hz over the period of use.
Resonance factor
V
R
Factor specifying the torque increase
at resonance
Temperature
T
a
°C
Ambient temperature of the coupling
in operation
Damping coeffi-
cient
ψ
Psi
Damping parameter
© Siemens AG 2015