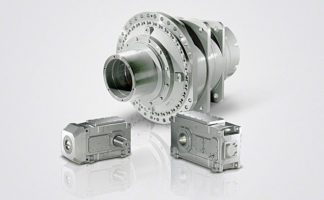
FLENDER Standard Couplings
技术信息
2/2
Siemens MD 10.1 · 2015
2
■
概述
Shaft misalignment
Shaft misalignment is the result of displacement during assem-
bly and operation and, where machines constructed with two ra-
表盘轴承每个都刚性耦合,会导致高负荷 -
ing placed on the bearings. Elastic deformation of base frame,
foundation and machine housing will lead to shaft misalignment
which cannot be prevented, even by precise alignment.
Furthermore, because individual components of the drive train
在运行期间以不同方式加热,MA-热膨胀
Chine外壳会导致轴不对。
Poorly aligned drives are often the cause of seal, rolling bearing
or coupling failure. Alignment should be carried out by specialist
人员按照西门子的操作说明。
根据有效轴未对准的方向,区分:
Axial misalignment
Radial misalignment
Angular misalignment
Couplings can be categorized into one of the following groups:
•
Single-joint couplings
Couplings with flexible elements mainly made of elastomer
材料。轴未对准导致变形
弹性体元素。弹性体元件可以吸收轴
轴向,径向和角度的变形不对准
方向。容许偏差的程度depends
在耦合尺寸,弹性体的速度和类型
元素。
单个关节联轴器不需要适配器,并在其中
fore short versions.
• Example:
In the case of a RUPEX RWN 198 coupling with an outer diam-
198毫米的速度和1500 rpm的速度,允许的径向
错位是
δ.
K
r
= 0.3 mm.
•
双关节联轴器
双关节联轴器are always designed with an adapter. The
两个关节水平能够吸收轴向和角度的错位 -
ment. Radial misalignment occurs via the gap between the
two joint levels and the angular displacement of the joint lev-
els. The permitted angular misalignment per joint level is fre-
非常约0.5°。允许的轴错位
可以通过适配器的长度调节耦合。如果有
are more than two joint levels, it is not possible to define the
position of the coupling parts relative to the axis of rotation.
(较少使用的平行曲柄联轴器是前的
ception)。
• Example:
ARPEX ARS-6 NEN 210-6 coupling with a shaft distance of
160.mm with a permitted radial misalignment of
δ.
K
r
= 1.77 mm(每个接头级0.7°的角度)。
Restorative forces
Shaft misalignment causes restorative forces to act on the cou-
由位移刚度确定的轴
of the coupling. These restorative forces are frequently compar-
atively weak and can usually be disregarded. Where bearings or
轴处于重载,恢复力应为
taken into account.
* b0'43b ;; b33335
.
D
* b0'43b ;; b33336
.
U
* b0'43b ;; b33337
.
Z
K
r
g_md10_xx_00014
.
U
* b0'43b ;; b33338
©Siemens AG 2015