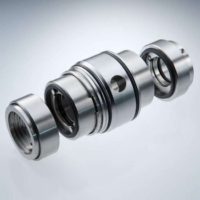
32
Ring type joints
Features
Ring type joints are manufactured
according to ASME B16.20 (2007)
standards and to API specifcation 6A and
17B. Careful control of all manufacturing
processes ensures correct surface
hardness to give a good seal without
damaging flange connections.
Advantages
• Secure sealing action through metal-to-
metal contact for reliable sealing in high-
pressure applications
• They are used in the oil field on drilling
and completion equipment and in
downstream refinery applications. Ring
type joints are also commonly used
on extremely high-pressure valves and
pipework assemblies, along with some
high integrity pressure vessel joints
Operating range
ASME B16.47 series A/B (ANSI B16.5):
class 150 ASME B16.20 (API 6A): class
2,000
材料
RTJs are available in soft iron, 304 and
316 stainless steels as standard. Other
materials are available on request.
Functional description
Under axial compressive load, ring type
joints plastically deform and flow into the
irregularities of the flange groove. Since
the load bearing area of the ring type
joint is relatively small, very high surface
stresses result between the sealing faces
of the ring type joint and the groove. These
stresses are further increased on the style
RX and BX rings which allow very high
internal pressures to be sealed. Since ring
type joints are solid metal, their recovery
characteristics are poor. The seal is
maintained by the action of axial load upon
the gasket.
Forms of supply
RTJs are available to suit all ASME and
DIN flanges from stock – ½" to 36"
and 15 mm to 900 mm. Larger size and
special requirements are available to order.
Standards and approvals
All ring type joints are manufactured
according to API standards, thereby
providing certified reliability.
Recommended applications
• Oil and gas industry
• Petrochemical industry
• Power plant technology
• Corrosion resistance is dependent upon
the choice of ring material
• Flange connections
• Pipe connections
Buralloy ring type joint 2961
Material
Identification
DIN specification
DIN material No.
B.S.
AIS-ASTM UNS
Maximum hardness
Brinell HB
Rockwell B HRB
Soft iron
D
–
1.1003
–
–
90
56
Low carbon steel
S
R st 37.2
–
–
–
120
68
F5
F5
5 Cr 0.5 mo
1.7362
–
A 182FS
130
72
SS 304
S304
X5Cr Ni 18
1.4301
304S15/16/13
304
160
83
SS 304L
S304L
X2 Cr Ni 18.9
1.4306
304S11
304L
160
83
SS309
S309
X15 Cr Ni Si 20.12
1.4828
304S24
309
160
83
SS 316
S316L
X5 Cr Ni Mo 18.10
1.4401
316S16
316
160
83
SS 316L
S316L
X2 Cr Ni Mo 18.10
1.4404
316S11/13
316L
160
83
SS 316Ti
S316Ti
X10 Cr Ni Mo Ti 18.10
1.4571
320S31
316TI
160
83
SS 321
S321
X10 Cr Ni Ti 18.9
1.4541
321S12/49/87
321
160
83
SS 347
S347
Xl0 Cr Ni Nb 18.9
1.4550
347S31
347
160
83
SS 410
S410
X6 Cr 13
1.4000
410S21
410
170
86
254SMO
S 254
X1 Cr Ni Mo Cu N 20.18.7
1.4547
S31254
180
89
Duplex
S 803
X2 Cr Ni Mo N 22.5.3
1.4462
31853
S31803/32205
230 approx.
99
Super duplex
S 750
X2 Cr Ni Mo N 25.6.3
1.4410
S32750
230 approx.
99
Aluminium
AL 1050
Al 99.5
3.0255
1B
A91050
30
–
Silver
Ag
–
–
–
28 (HV)
–
Copper
Cu
SF-CU
2.0090
Cl06
C12200
80 approx.
–
Brass
CuZn37
Cu Za 37 (M563)
2.0321
CZ108
C27200
60 approx.
–
Nickel 200
Ni 200
Ni 99.2
2.4066
3072-70 NA11
NO2200
110
62
Monel
®
400
N 400
Ni Cu 30 Fe
2.4360
3072-76 NA13
NO4400
150
80
lnconeI
®
600
N 600
Ni Cu 15 Fe
2.4816
3072-76 NA14
NO6600
150
80
lnconel
®
625
N 625
Ni Cr 22 Mo 9 Mb
2.4856
3072 - 76年NA21
NO6625
150
80
Incoloy
®
800
N 800
X10 Ni Cr Al Ti 3220
1.4876
3072-76 NA15
NO8800
150
80
Incoloy
®
825
N 825
Ni Cr 21 Mo
2.4858
3072-76 NA16
NO8825
195
92
Hastelloy
®
B2
B2
Ni Mo 28
2.4617
NI0665
230
99
Hastelloy
®
C276
C276
Ni Mo 16 Cr 15W
2.4819
NI0276
210
95
Type 904
N 904
X1 Ni Cr Mo Cu 25.20.5
1.7440
904S13
N08904
160
83
Titanium
Ti2
Ti 99.8
3.7025
TA2
R50400
–
–