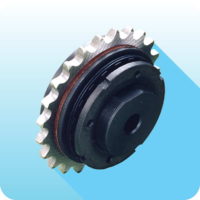
15
50
100
150
200
250
1,25
1,20
1,15
1,10
1,05
1,00
0
20
40
60
80
100
0
25
50
75
100
80
60
40
20
0
C'
nom
=
C.C.
2,5
C
nom
≥
C'
nom
C
nom
=
C
spunto
1,5
C
nom
≥
C’
nom
C
nom
>
C
nom
>
•
f
•
f
T
•
f
D
•
f
K
•
f
T
•
f
D
9550
•
P
9550
•
P
n
n
For pre-selec
Ɵ
on of the coupling's size you can use the generic formula indicated on page 6.
The GTR coupling will accomodate momentary peak torque "C.C." of 2,5
Ɵ
mes than nominal torque.
If the C.C. is higher than 2,5
Ɵ
mes than the nominal torque, it is necessary to choose the coupling using the following formula:
The nominal torque indicated on the catalogue for GTR coupling refers to the sta
Ɵ
c torque 2
Ɵ
mes lower than the nominal torque, with
service factor f=1.5. On the contrary, if the sta
Ɵ
c torque of the motor is two
Ɵ
mes higher than the nominal one, it is possible using the
following formula:
Having calculated the theore
Ɵ
cal nominal torque (C'nom), so that the coupling can be sized correctly it is necessary, to compare the
e
ff
ec
Ɵ
ve technical characteris
Ɵ
cs of GTR (pages 8-9) and to choose the size able to transmit an e
ff
ec
Ɵ
ve nominal torque (Cnom) higher or
equal to the one found by the described formulae above.
Having established the size of the coupling to be used, it is possible to make other checks considering further parameters:
Where:
C’
nom
=定理
Ɵ
c nominal torque of the coupling
(纳米)
C
nom
= e
ff
ec
Ɵ
ve nominal torque of the coupling
(纳米)
C.C.
= peak torque
(纳米)
Where:
C’
nom
=定理
Ɵ
c nominal torque of the coupling
(纳米)
C
nom
= e
ff
ec
Ɵ
ve nominal torque of the coupling
(纳米)
C
spunto
= peak torque
(纳米)
Direc
Ɵ
on factor (f
D
)
1 = one-direc
Ɵ
on rota
Ɵ
on
2 = alternate rota
Ɵ
on
Load factor (K)
1,5
= con
Ɵ
nuous load
2
=
discon
Ɵ
nuous load
1,5÷2 = machine tool
2,5÷4 = shock load
Dove:
C
nom
= nominal torque of the coupling
(纳米)
f
= service factor (pag.5)
f
T
= thermic factor (gra
fi
co 1)
f
D
= direc
Ɵ
on factor
f
K
= load factor
n
= speed
[Rpm]
P
= applied power
[Kw]
Opera
Ɵ
ng temperature
[°C]
Thermic factor f
T
1. Thermic factor (f
T
) in func
Ɵ
on
of the opera
Ɵ
ng temperature [°C]
GTR & GTR/DBSE - torsionally rigid coupling: addi
Ɵ
onal informa
Ɵ
on
Once the torque to be transmi
Ʃ
ed has been
calculated and veri
fi
ed , it is necessary to consider
fl
exibility o
ff
ered by the chosen coupling with
actual misalignments present between the sha
Ō
s
to be connected.
It is important to note that the axial and
radial misalignments permi
Ʃ
ed are inversely
propor
Ɵ
传统(one increases the other must
decrease). If all types of misalignment are present
in the assembly it is important the total sum as
a percentage to not exceed 100% as shown in
graphic 2.
Axial misalignments
x [%]
Radial misalignment
K [%]
2. Allowed ra
Ɵ
o between misalignments [%]
DIMENSIONING